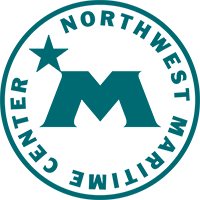
For the next week, we will camp out in the boat shop at the Northwest Maritime Center in Port Townsend, Washington, breathing epoxy fumes and embedding fiberglass in our fingers. This is the almost-final step towards finishing the wood-strip canoe started ten years ago by our friend, Matthew Mattson.
Matthew started this project as a senior in high school. He built a form, then applied strips of cedar to the form, then went to college, then moved to New York to be an architect. His parents consented to store the unfinished boat in the family garage, not realizing this would be a long-term commitment and would occupy the space otherwise given over to a ping-pong table.
Janell and I have an affinity for boats. (Question: How many boats are enough? Answer: just one more) We have a yard full of canoes and kayaks. We were targeted identified as a couple likely to finish the boat—and get it out of the garage. We said yes.
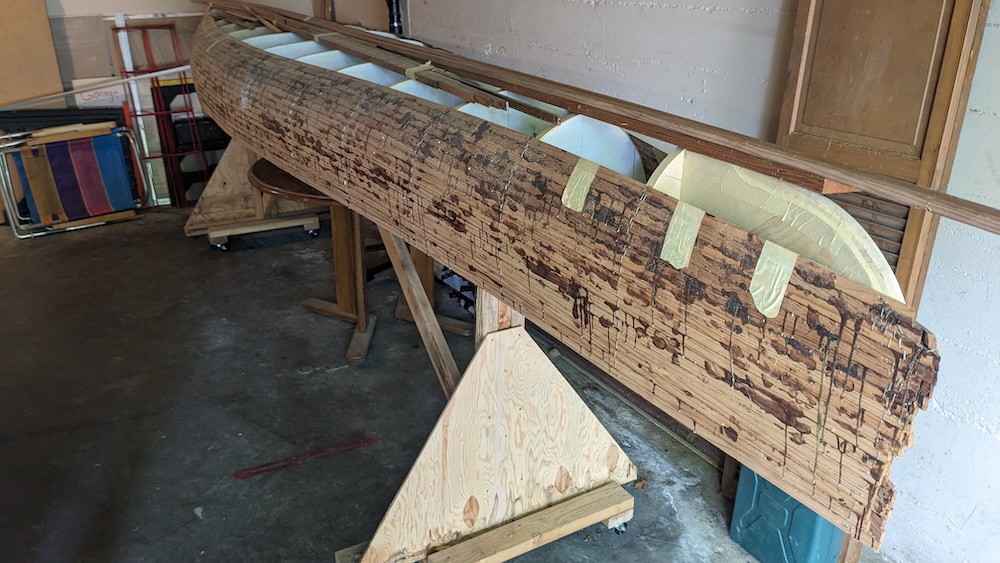
Here is the boat we started with. The form is STURDY and Matthew had finished a good portion of the stripping. We applied our enthusiasm to the rest of the project. Here’s a picture of how it looks right now.
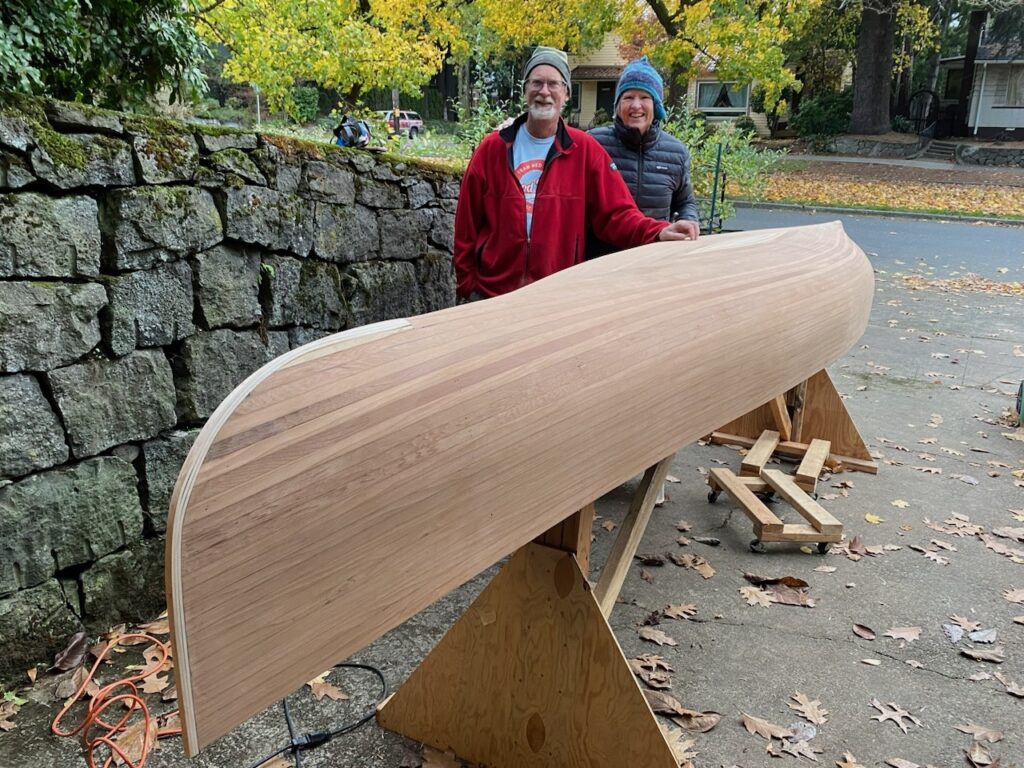
It is a thing of beauty. It has beautiful lines and curves and the strips of cedar give it a sense of authenticity. There are flaws: staple holes, gaps between the strips, gouges, and blemishes. But it is hand-built and one of a kind.
Being part of Matthew’s project is an honor and brings us a great deal of satisfaction. We’re not always sure what we are doing and often shrug our shoulders and state: “The next time we build a boat, we’ll do this differently…“
Applying a coat of fiberglass to a boat will give it strength but requires epoxy resin. Epoxy requires a chemical reaction between the resin and the hardener (a catalyst) and, like all good chemical reactions, performs best at a specific range of temperatures. So the room needs to be between 68 and 80 degrees Fahrenheit. You can’t use gas heaters as these release hydrocarbons into the air, which inhibits the epoxy reaction. And the reaction releases fumes, so the room needs to be ventilated. We looked long and hard for a room that would satisfy these requirements, but couldn’t find any in Portland.
Northwest Maritime Center to the rescue! We have rented space in their boat shop for the week and are enthusiastically looking forward to their expertise and guidance. However, this means we need to transport the boat from Portland to Port Townsend. Because it doesn’t have any fiberglass, it must remain on the form. It’s heavy!
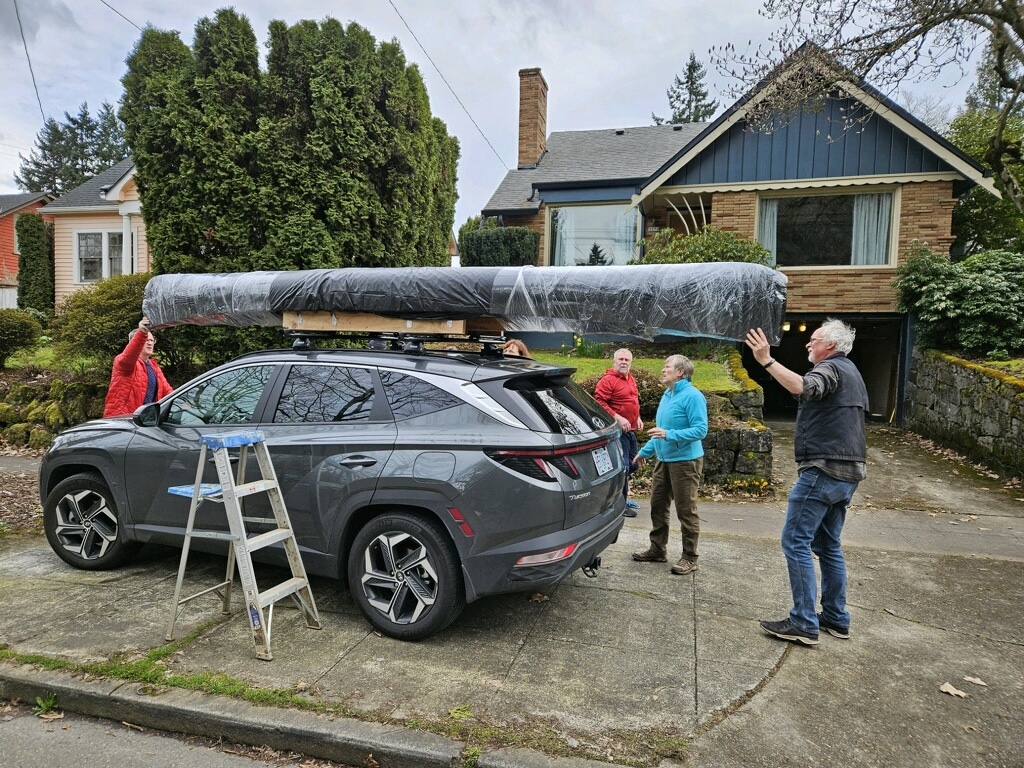
Janell and I wrapped it up in plastic, cut off the legs, and attached two-by-six skids to the sides so it would ride on the carriers on the top of our Hyundai Tucson. Next, we invited some OOPSters to help us lift, carry, and attach the boat to the car. Thanks Al, Sara, Brenda, Robin, and Paul!
Our friend Rich showed up Saturday night, and we got rolling Sunday morning. We made a brief stop in Tacoma to see our delightful (and above average grandchildren) (and their parents) then arrived at Port Townsend at 3:30 pm. Here we met our new friend Joel, who showed us where to place the boat.
The trick was getting the (heavy) boat off the top of the car and into the shop. There are only three of us: Rich, Janell, and I. Three versus the (heavy) boat. We are struggling until Joel comes out and suggests the forklift. We didn’t realize that was an option.
Joel gets the forklift, and the problem is solved! We get the boat on the ground and carry it to it’s new home for the next week.
Joel and Rich take a critical look at the boat and point out several flaws that will need fixing. But Janell and I are game for an adventure and looking forward to the experience.

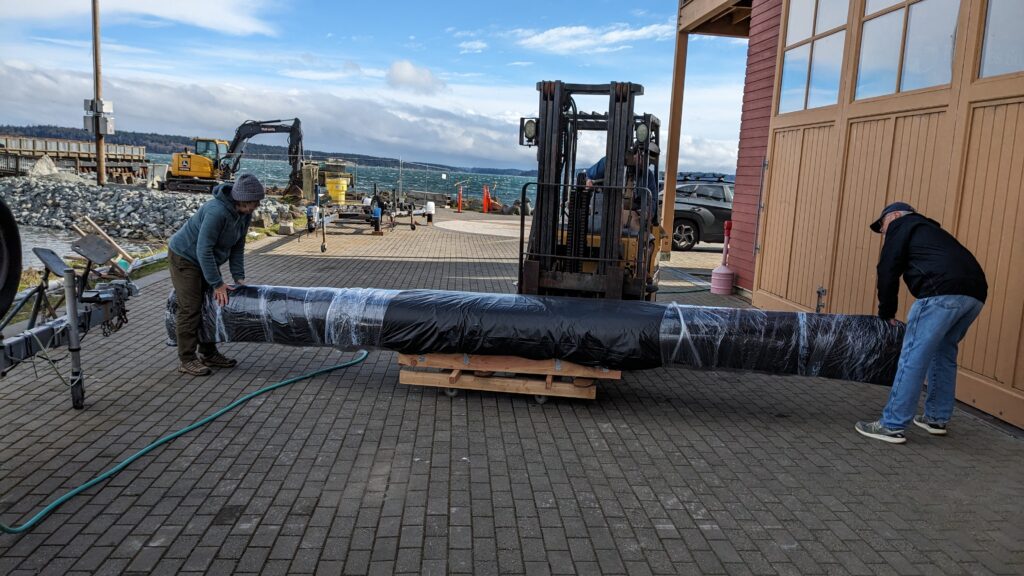
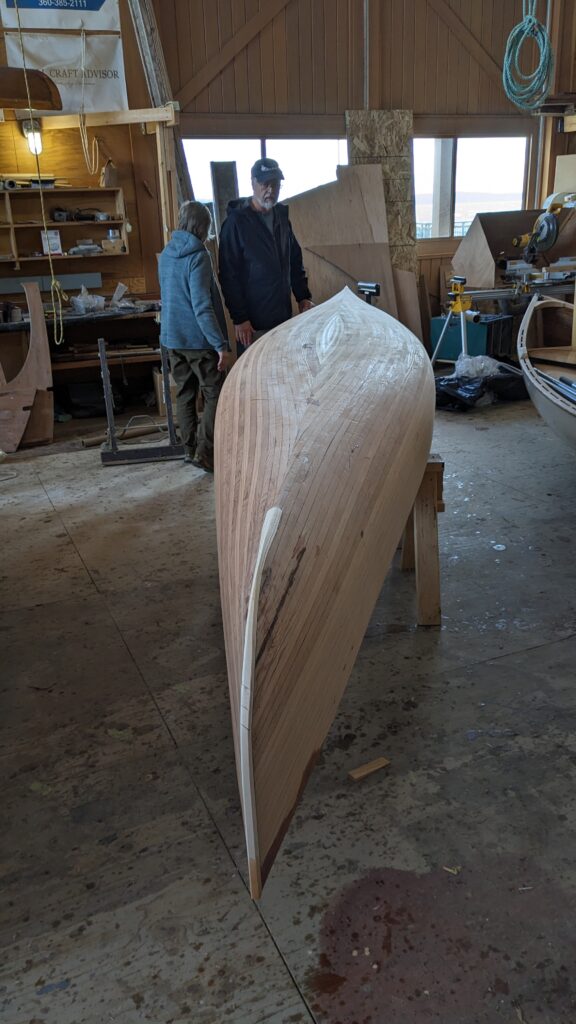
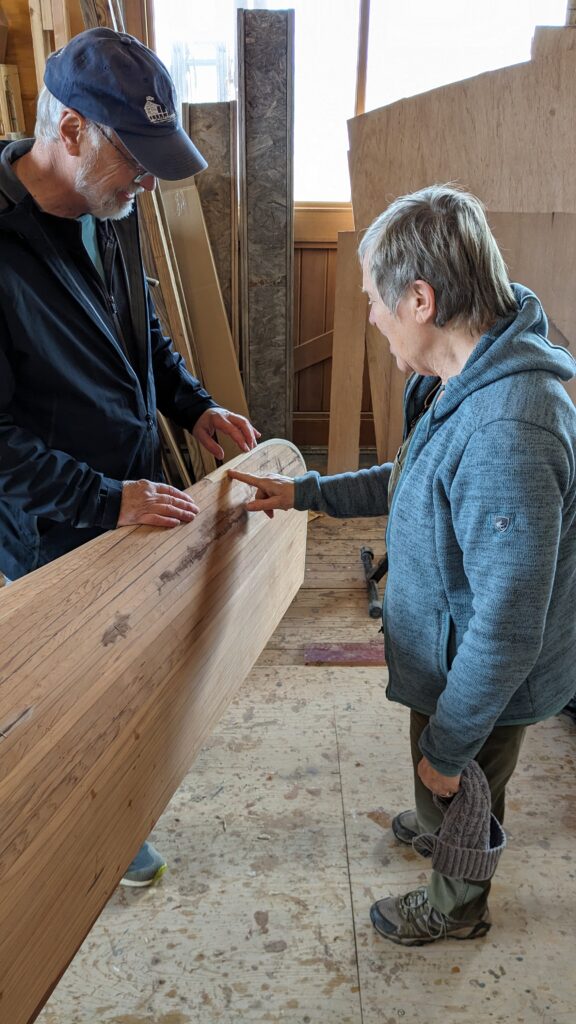